bole-The processing capacity of a magnetic polisher is affected by many factors, including equipment specifications, workpiece characteristics, process parameters, etc. To accurately evaluate its single processing volume, a systematic analysis is required from the following aspects:
Equipment Specifications
The processing capacity of a magnetic polisher is mainly determined by the size of its working chamber. Taking the standard model as an example, the common working chamber volume is between 5-20 liters. For example, a 10-liter capacity model has a working chamber diameter of about 300mm and a height of 250mm. However, the actual loading capacity is usually 60-70% of the chamber capacity to ensure sufficient movement of the polishing medium and the workpiece.
Workpiece characteristics
The size, shape, and material of the workpiece directly affect the single processing volume:
Small workpieces (such as screws, jewelry): thousands of pieces can be processed at a time
Medium-sized workpieces (such as tools, mold parts): hundreds of pieces can be processed at a time
Large workpieces (such as mechanical parts): may only be processed in a few dozen pieces at a time
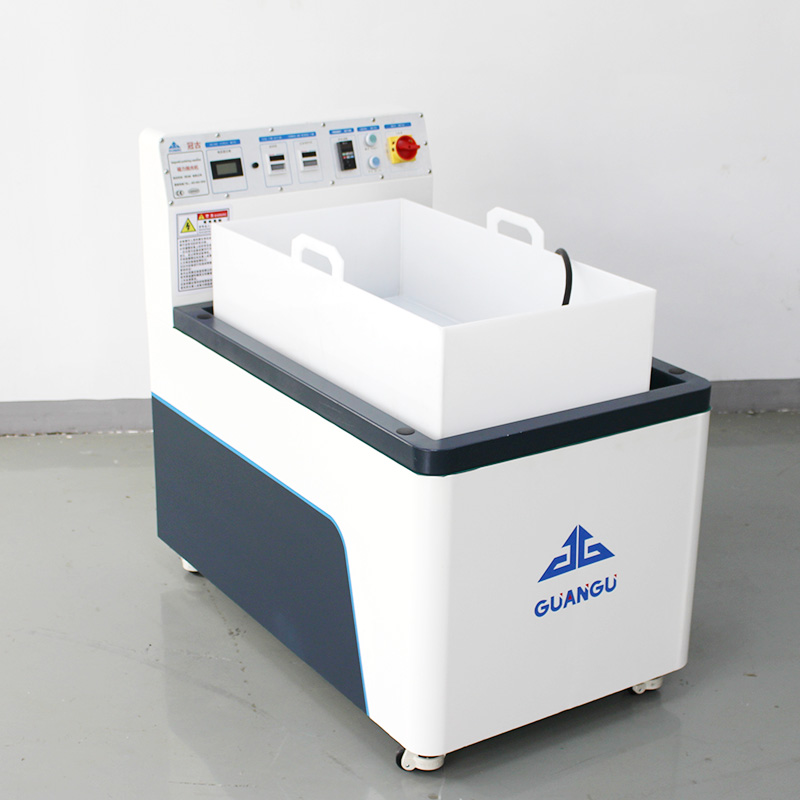
Polishing medium
The volume ratio of the medium to the workpiece is usually 2:1 to 5:1. For example, in a 10-liter working chamber, 4-6 liters of medium are required, and the remaining space is used for workpiece loading. The choice of medium (shape, size, material) will also affect the loading capacity.
Process parameters
Speed: affects the movement trajectory of the workpiece and the polishing efficiency
Processing time: related to the number of workpieces and polishing requirements
Magnetic field strength: determines the polishing strength and uniformity
Actual case analysis
Take a certain automotive parts manufacturer as an example, using a 15-liter magnetic polishing machine to process bearing rollers (diameter 8mm):
About 5,000 pieces can be processed at a time
Processing time: 45 minutes
Surface roughness reduced from Ra1.6μm to Ra0.2μm
Dimension change controlled within ±0.01mm
Production efficiency optimization suggestions
Reasonably match the workpiece size to improve the loading rate
Optimize the medium ratio to ensure the polishing effect
Use an automated loading and unloading system to reduce downtime
Regularly maintain the equipment to maintain the best working condition
Precautions
Avoid overloading and affecting the polishing quality
Workpieces of different materials should be handled separately
Regularly replace the polishing medium
Monitor the temperature changes during the processing process
Summary: The single processing volume of the magnetic polishing machine needs to be evaluated according to the specific situation. It is recommended that users conduct small batch tests before actual use to determine the best process parameters and loading amount to achieve the best polishing effect and production efficiency. At the same time, a complete quality control system should be established to ensure the stability and consistency of processing quality.